Biopolymers are the future of food packaging
We have to stop using our longest-lasting material for our most temporary commodity goods.
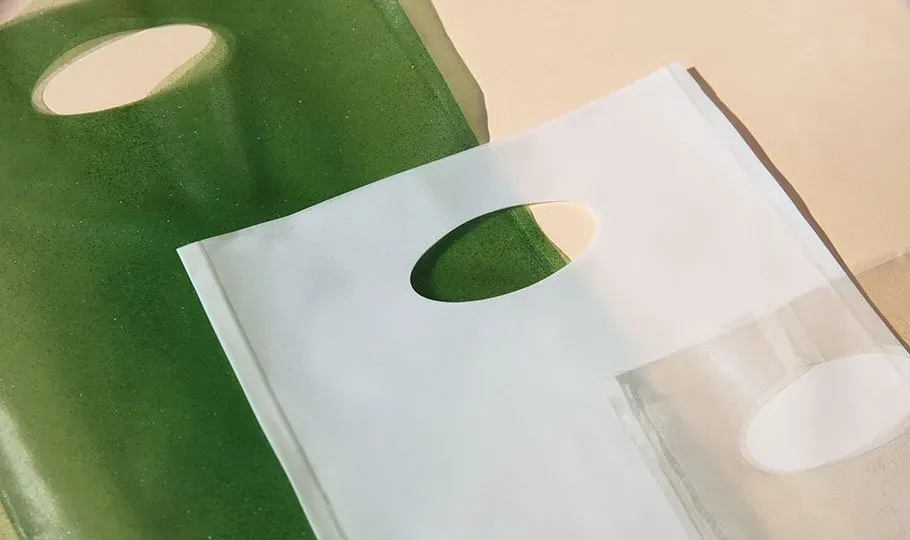
If I could wave a magic wand and make our consumer-obsessed culture do a Uno reverse and instil in our political and business leaders the courage to implement the policies we need to address the waste crisis, this blog and newsletter wouldn't need to exist.
And yet, global plastic pollution is worsening, and international efforts to regulate it are floundering.
The UN-backed treaty negotiations aimed at curbing plastic waste have stalled, as economic interests override environmental reality. Meanwhile, plastic production is set to nearly double by 2050, and millions of tonnes of waste continue to flood our ecosystems.
Of all plastics produced worldwide today, nearly 40% are used for food and drink packaging.
If we insist on not changing our behaviour and feeding our convenience obsession, we must stop using our longest-lasting materials for our most temporary commodity goods, such as food and beverage packaging.
From nature, back to nature
Amidst all this gloom is a glimmer of bloom. And while political solutions remain elusive, science is offering something tangible: biopolymers.
Biopolymers—compostable materials derived from plants, animals, and microorganisms—are increasingly proving to be a viable alternative to fossil-fuel-based plastics. Unlike conventional fossil-fuel-derived plastics that persist in the environment for centuries (never breaking down, only breaking up into smaller and smaller microplastics), biopolymers can break down within weeks, turning into organic matter instead of microplastic pollution.
From nature, back to nature.
Scientists and innovators are developing biopolymer-based films with strong barrier properties against moisture, oxygen, and carbon dioxide—key factors in preserving food freshness. For instance, pectin-based films, derived from fruit peels, have been shown to extend the shelf life of vegetables like capsicum by up to 15 days.
These films, often combined with natural substances like castor or clove oil, offer a sustainable alternative to the synthetic wax coatings currently used to enhance produce longevity.
Companies like Sway, NBCo, Notpla, Shellworks, and Uluu here in Australia are leading the charge toward a future free from fossil plastics, developing materials that are regenerative by design.
NBCo's 'disappearing’ bottle
At the 2025 World Economic Forum in Davos, NBCo unveiled its ‘disappearing’ fibre-based bottle, designed to be up to 99% recyclable and biodegradable. Made from fast-growing renewable plant-based feedstocks like bamboo and agricultural waste, the bottle is engineered for circularity with a decentralised manufacturing approach that shortens supply chains, cuts emissions, and supports local economies.
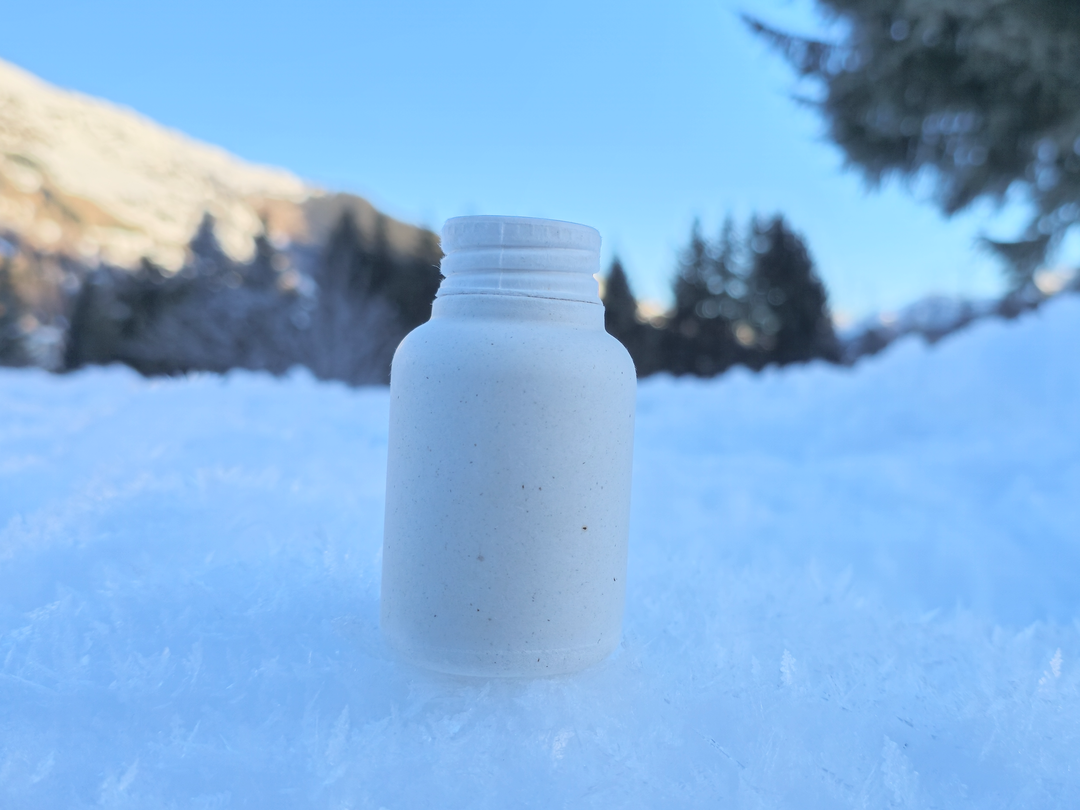
The bottle is designed to be recycled in existing paper streams, keeping waste out of landfills and ecosystems. Biodegradability testing in soil and seawater is expected in early 2025.
NBCo combines plant fibre strength with precision moulding, bio-additive enhancements, and advanced testing to ensure performance under real-world conditions. The company launched its Fast Forward 50 initiative, providing free trials to 50 brands to accelerate adoption and demonstrate the bottle’s scalability as a viable plastic alternative.
A potential solution to the soft plastics scourge
After the collapse of soft/flexible plastics recycler REDcycle here in Australia, there hasn't been an end-of-life solution that works at scale for these versatile but problematic materials.
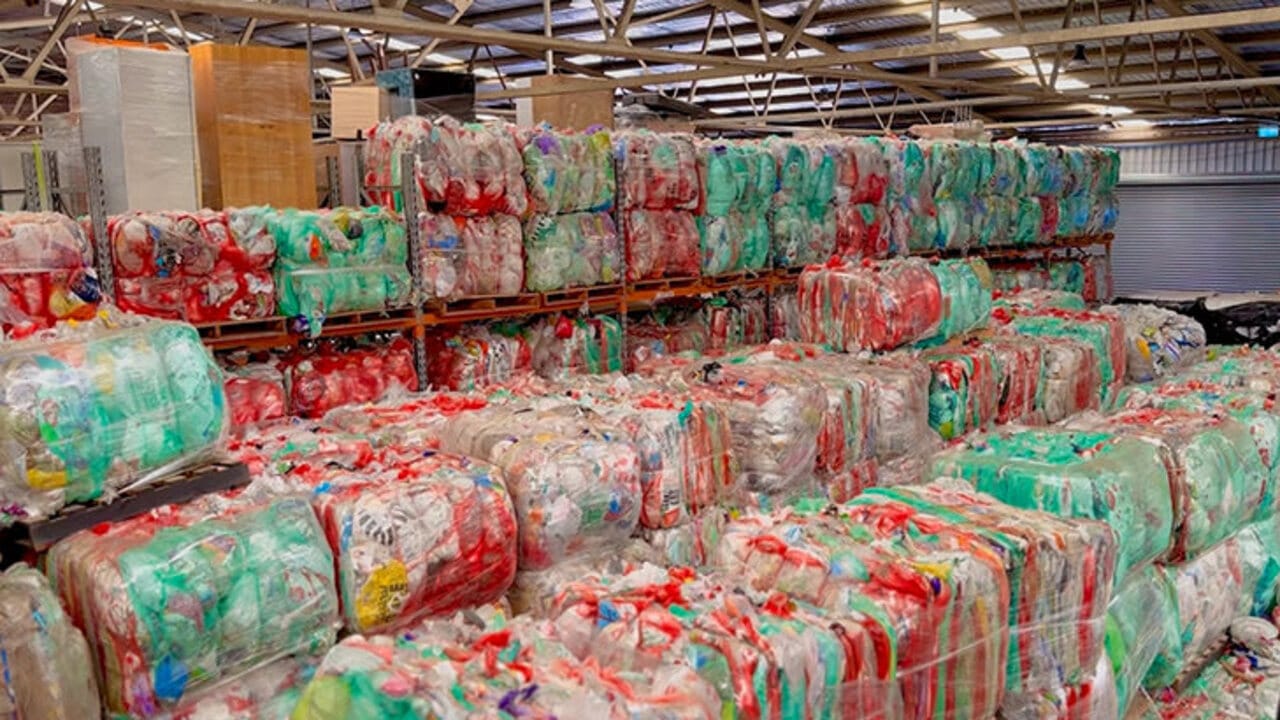
While flexible plastics make up 45% of all plastic packaging placed on market, they represent only 24% of all plastic packaging recovered.
A materials expert I spoke to insists that there is no viable recycling path for these materials. At best, the offtake is downcycled into park benches, not exactly an exciting TAM. The process is incredibly expensive and complicated. This expert told me that just 1% of PVC in the feedstock corrodes the machinery, making it prone to breakdown and fire. Both of these issues, it seems, played a role in REDcycle's collapse.
Some exciting biopolymer startups are tackling this problem, with cellular-based materials leading the charge.
PHA has been a quiet achiever in this space. It can be made using a variety of organic feedstocks (including food, agricultural, and cooking oil waste). The manufacturing process involves millions of microbes feasting on the nutrients of the feedstock. Much like humans put on weight when we overeat, these microbes bulk up with the biopolymer Polyhydroxyalkanoates.
PHA’s potential lies in the fact that the pellets can be used on existing plastic moulding machinery. It looks and feels like plastic, is shelf-stable, and can even be dishwasher-safe. The difference is that if it ends up in the environment or a compost heap, the microbes will see it as a food source and break it down.
Until recently, PHA has shown the most promise in blow moulded applications, but that's changing... fast.
CJ Biomaterials recently launched two new PHA-based compounds, PHACT™ CA1270P and CA1240PF, designed for flexible packaging films as a compostable alternative to traditional plastics. Developed in partnership with NatureWorks, these bio-based materials offer high performance while significantly lowering carbon footprints.
They help divert food waste from landfills, reducing methane emissions, and are industrially compostable—with potential for home compostability. With strong durability and competitive pricing, these materials could provide a scaleable and viable alternative to without compromising on packaging functionality.
Biopolymers can unlock a biocircular materials economy
Despite their promise, scaling biopolymers for mass adoption is a challenge. Production processes are still being optimised to improve mechanical stability and thermal resistance, making them more commercially viable.
But, momentum is building.
Some expect the emerging biopolymer industry is projected to partially replace fossil-based plastics by 2050, with some estimates suggesting biopolymer production could rival conventional plastic output between 2035 and 2040.
I certainly hope so and will be doing my best to beat the drum for this important hack to our materials economy.
The plastic industry has long promoted recycling as the answer to waste, but in reality, only 9% of plastics ever produced have been recycled. The rest end up in landfills, incinerators, or the natural environment (and in us).
For a closed-loop system (such as our planet) to remain in balance, all waste must be a food source for something else and metabolised without accumulation or resource depletion. Ecosystems fall out of balance when the waste being created grows exponentially or the ability to process that waste is diminished.
A truly circular economy cannot be built on plastic—it requires materials that biodegrade and bioassimilate safely, without toxic residues, and nourish the planet rather than pollute it.
Biopolymers represent more than just an alternative—they’re a fundamental rethinking of how materials should work in harmony with nature and hold the potential to be the unlock we need for a biocircular materials economy based on soils, not oils.
And as they move from lab breakthroughs to large-scale solutions, they just might offer the most practical path forward in the fight against plastic pollution.