The Paperisation of Everything
How pulp and fibre are redefining sustainable packaging
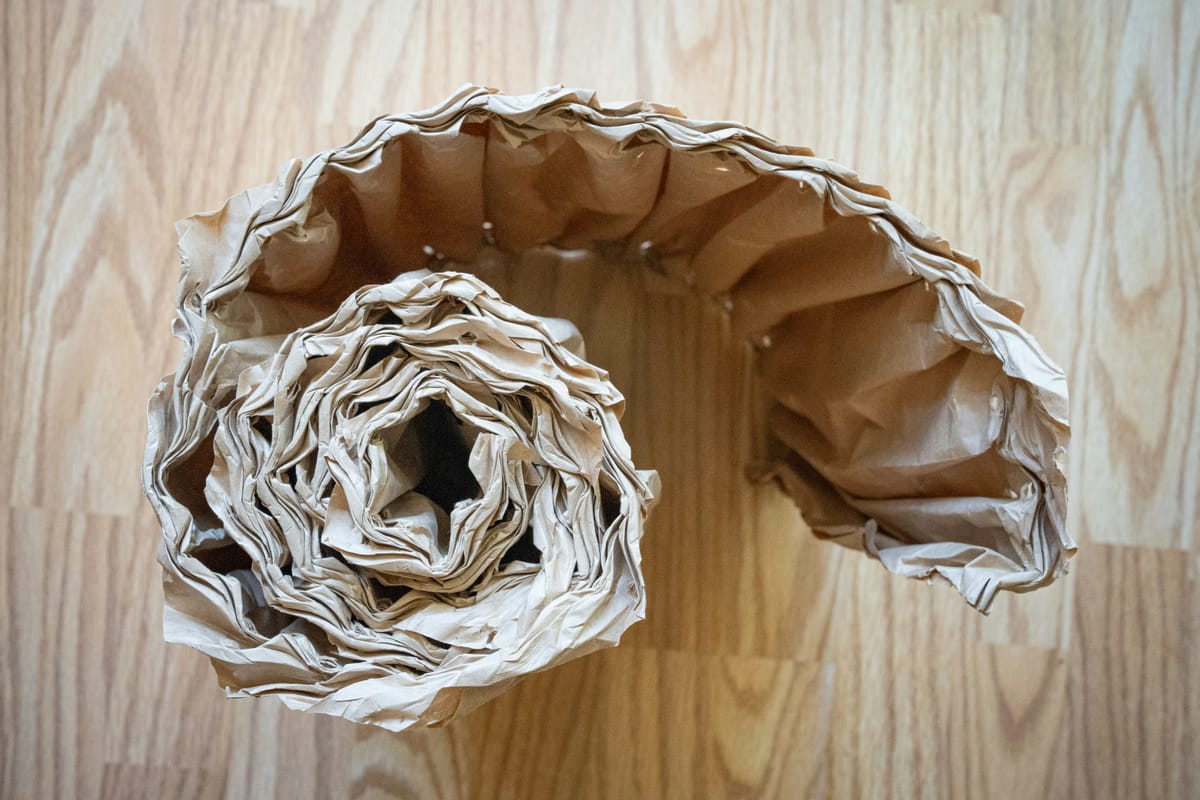
The notion that we can recycle ourselves out of the plastics crisis is proving to be a stubborn and all-pervasive myth.
From fossil fuel lobbyists at INC-5 through to circular economy advocates at sustainability conferences, there is a common view that all we have to do to solve this crisis is increase our global recycling rates from the tragically low current baseline of 9%.
I get the appeal, it sounds simple and doable. When, really, it is simplistic and inadequate.
It doesn't account for the fact that plastic (unlike Aluminium) can't be infinitely recycled. Nor that the recycled plastic is generally downcycled to a poorer quality material. And given the collection, sorting and processing costs, recycled plastic is often more expensive than virgin plastic.
And we wonder why recycling rates remain so low, and the production of virgin plastic continues to climb.
Besides, do we really want to give plastic a second, third, or fourth chance at life? So, it can leach endocrine-disrupting chemicals and shed microplastics a second, third, or fourth time?
I don't think so.
Plastic's ubiquitous presence throughout our supply chains and convenience-driven economy means we need to find and implement replacements... fast.
And given plastic's versatility, no one material is up to the task. It will take an array of existing and novel materials to plug the gaps.
If we're going to learn from the mistakes that led to this plastic crisis, the characteristics required for us to shift to a bio-circular materials economy are materials that:
- Can be made from bio-based recycled and renewable feedstocks
- Are toxin and contaminant free
- Are cheap and fast to manufacture
- Have excellent performance characteristics
- Are versatile with a wide range of applications
- Are easy to recover and recycle
- Bioassimilate back into nature if they escape the waste cycle
We also need to ensure that we adhere to the principles of Materials Minimalism to ensure high recovery and recycling rates. This often means that we can't combine materials to match the performance of plastic. Each material will have to stand on its own two feet.
One such material is paper.
Yes, paper.
Paper, but not as you know it
Moulded pulp and fibre (such as egg cartons) have been around almost as long as plastic, but the new generation of moulded pulp and fibre is something else entirely. And it's this long history of R&D and usage that could pave the fastest path to commercialisation over comparable novel materials.
As the Sustainable Packaging Coalition highlighted in its inaugural Packaging Innovations Trends Report, fibre was one of the most prominent trends for 2024—and for a good reason.
Pulp has always been appealing thanks to its recyclability and biodegradability. However, until recently, its adoption was limited by performance and barrier challenges, which made it less viable for applications requiring moisture resistance or structural durability.
This is beginning to change. Fast.
Pulp Traction
While novel materials claim much of the limelight, there has been considerable innovation in moulded pulp and fibre that has made it the quiet achiever this year.
Advances in fibre technology, such as PulPac’s Dry Molded Fiber process that transforms generic pulp into nearly any three-dimensional shape, have meant they can achieve speeds comparable to plastic production while using minimal water.

The broader packaging industry is beginning to embrace fibre not just as a cardboard box substitute but as a versatile material for bottles, wraps, and more.
London-based Pulpex is another compelling example of the growing investment in fibre innovation.
Backed by brands like Diageo, the paper bottle company raised £20 million in Series C funding, underscoring the market’s confidence in pulp as a transformative material.
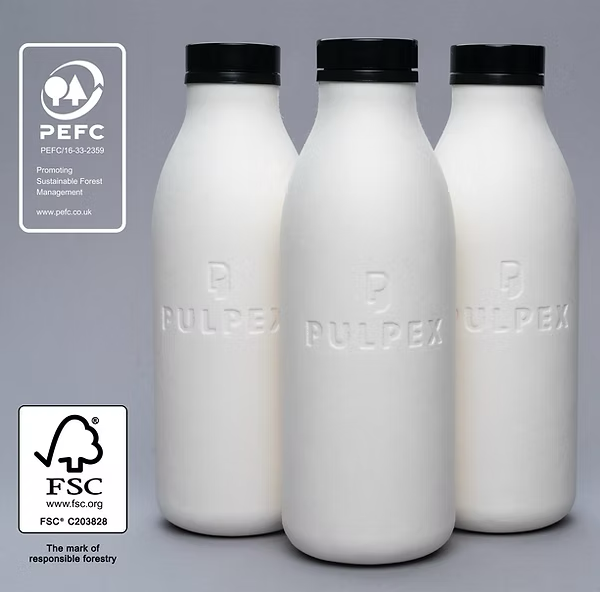
Pulp can also step in for plastic packaging of products that require an oil barrier. Upfield, has collaborated with several partners to develop a plastic-free, oil-resistant paper tub for its plant-based butter and spreads, aiming to cut over 25,000 tons of plastic waste annually.
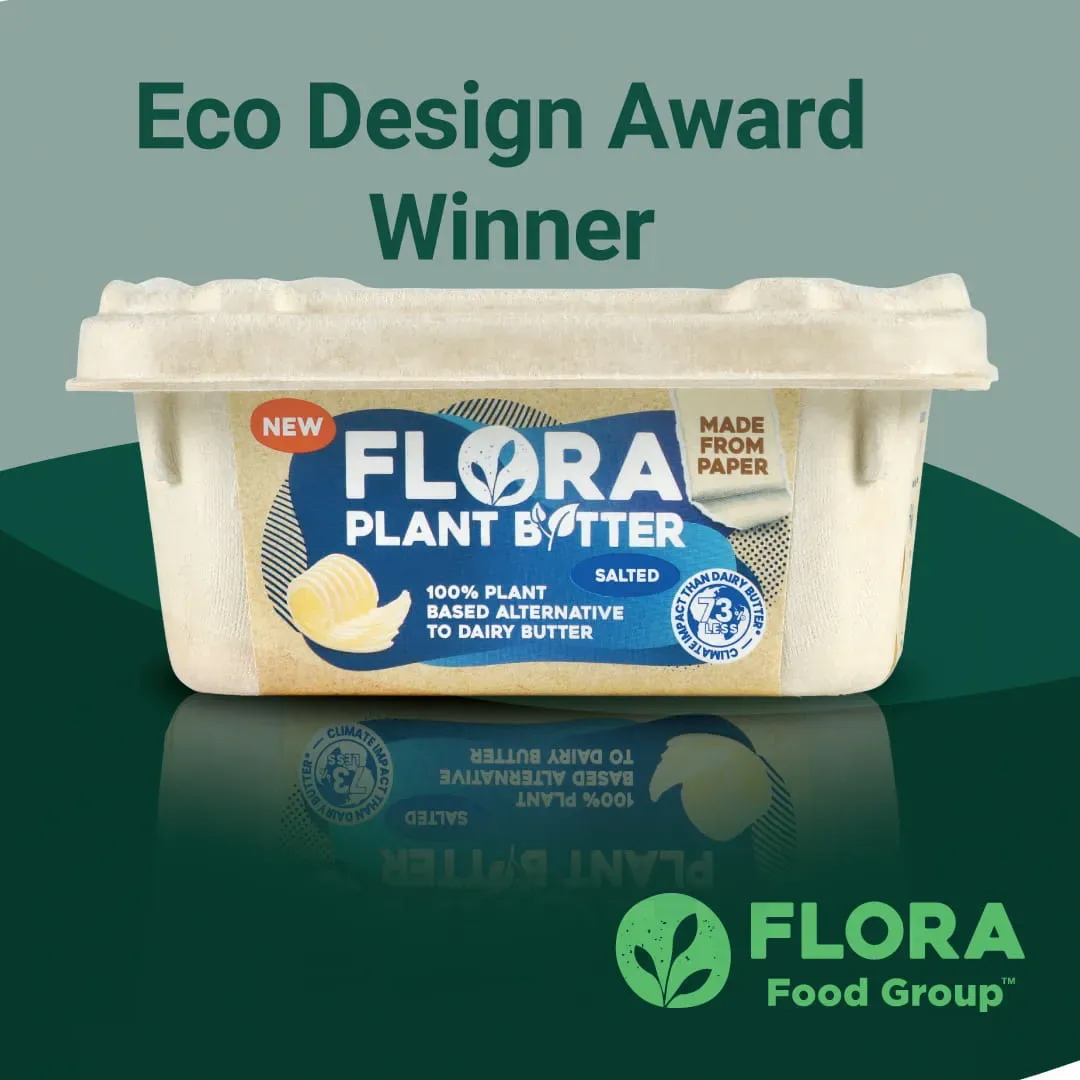
John Verbakel, Upfield’s head of R&D, told the Financial Times that while the paper tub’s carbon impact is currently similar to plastic, advancements in paper packaging efficiency are expected over time. He also highlighted the problem with plastic lifecycle assessments assuming that all plastic tubs are recycled—far from Europe’s actual 40% recycling rate.
The paper tub is set to achieve compostable certification by next year.
An alternative to the soft plastics menace
WestRock and Atlantic Packaging have teamed up to create Canopy, a fibre-based wrap designed to replace plastic shrink films on bulk food and beverage packs.
According to WestRock, this kraft paper wrap is recyclable in curbside programs, offering a practical and more sustainable alternative for packaging.
A key advantage of Canopy is its compatibility with existing shrink bundling lines. Operators can seamlessly integrate the paper wrap by feeding it through the same machinery used for plastic film, simply disabling the heat function. Once in place, Canopy is tightened and glued securely around the tray, ensuring that cans remain stable and protected.
Demonstrating the material’s durability, an entire pack can be lifted by the paper wrap without wrinkling or tearing. The wrap also supports high-quality printing, enabling brands to maintain impactful messaging and branding.
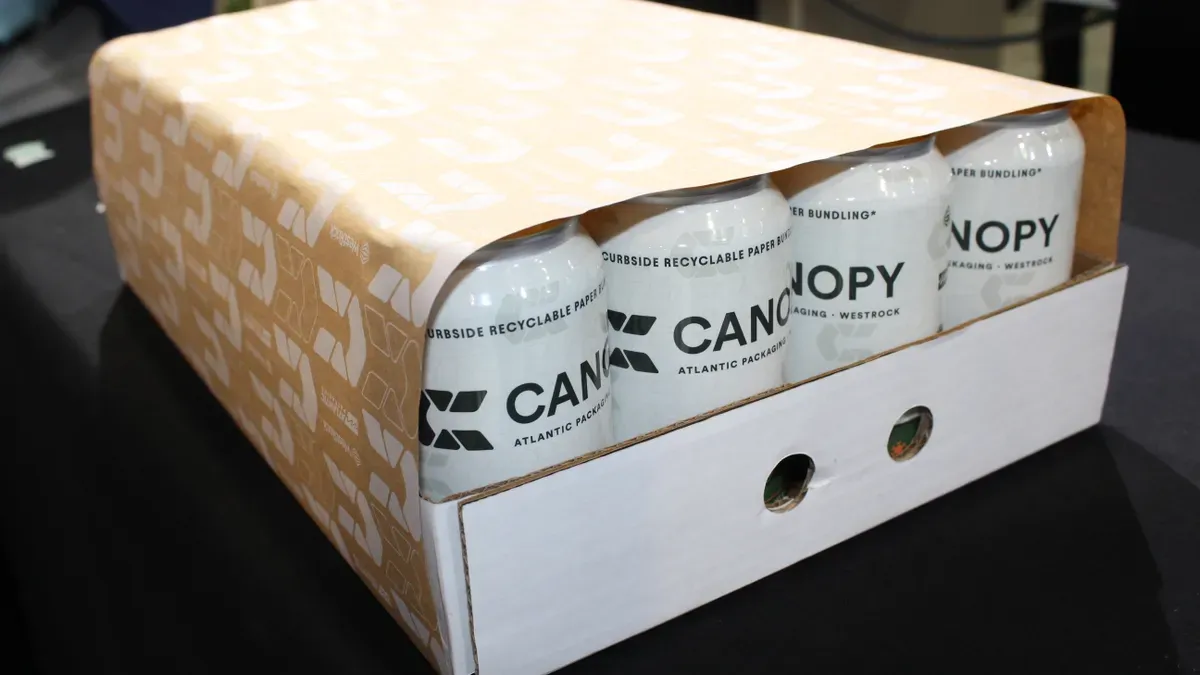
Clearer end-of-life pathways
Most moulded fibre and pulp products are compostable, as well as being fully recyclable through the paper waste recycling stream.
Unlike plastics, which are plagued by recycling inefficiencies, toxicity and pollution concerns, fibre-based materials boast clearer recycling pathways and are generally free from harmful additives.
And if these items do end up in the environment as fugitive items from the waste stream, they can assimilate and break back down into organic components without leaching toxic chemicals.
The clear end-of-life pathways combined with the innovations in cost, speed and performance mentioned above, make moulded pulp and fibre a compelling alternative to plastic across myriad use cases. However, both brands and consumers will need to watch out for pulp products that use plastics or toxic forever chemicals like PFAs as binding agents, or to make fibre products water and grease-resistant.
Fortunately, bio-based innovations such as Notpla’s seaweed-based coatings offer plastic and PFAs-free oil and water barriers for containers and packaging that won't contaminate recycling or compost waste streams, nor the environment in the case of fugitive litter.
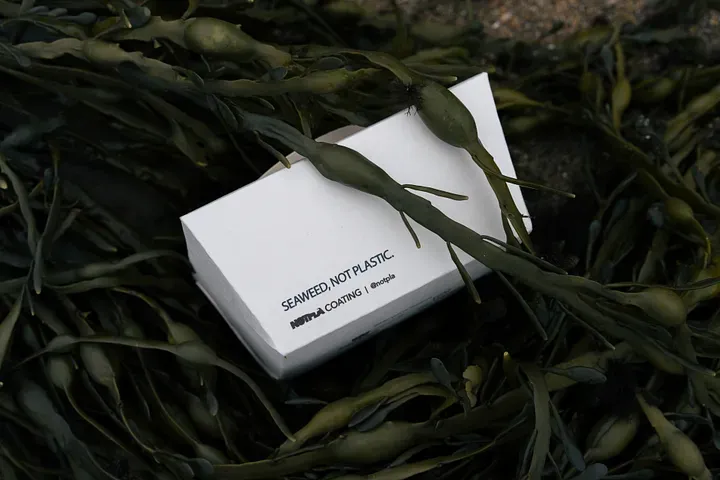
Sustainable sourcing
Scaling fibre-based alternatives to plastics won't be without its challenges.
Feedstock availability and sustainability are two critical hurdles that need to be cleared for long-term viability. Recycled or waste material is the ideal, but if the feedstock is cultivated, it should be from high-yield and low-impact sources.
While trees are a renewable resource and offer carbon sequestration benefits, forests must be managed responsibly to prevent overexploitation. Given their slow growth, relying solely on traditional timber-based pulp is unsustainable at scale.
Fortunately, innovators are addressing this by exploring diverse and renewable feedstock sources.
Recycled pulp, for instance, is gaining traction as a cornerstone of sustainable production. Meanwhile, agricultural byproducts like corn stover, as well as fast-growing grasses and other fibrous plants cultivated on marginal lands, are providing exciting alternatives.
These approaches not only reduce dependence on virgin wood but also create opportunities to repurpose waste and utilise underperforming agricultural spaces.
Paving the paper trail to a circular economy
To truly unlock fibre’s potential, industry stakeholders will need to focus on balancing innovation with sustainability.
Technologies that improve pulp’s performance characteristics must also align with regenerative practices in sourcing raw materials. The potential of agricultural waste and non-timber feedstocks is promising, but careful management is needed to ensure these resources deliver environmental benefits without unintended consequences, such as competition with food systems.
As fibre expands beyond its traditional territory, it could easily emerge as a linchpin in the quest for a circular materials economy. Its scalability, recyclability, and ability to adapt to a wide range of applications offer a glimpse of a future where packaging aligns more closely with regenerative principles.
With continued innovation and responsible sourcing, the paperisation of everything may soon be more than a trend—it could become the new standard for sustainable packaging.